[ad_1]
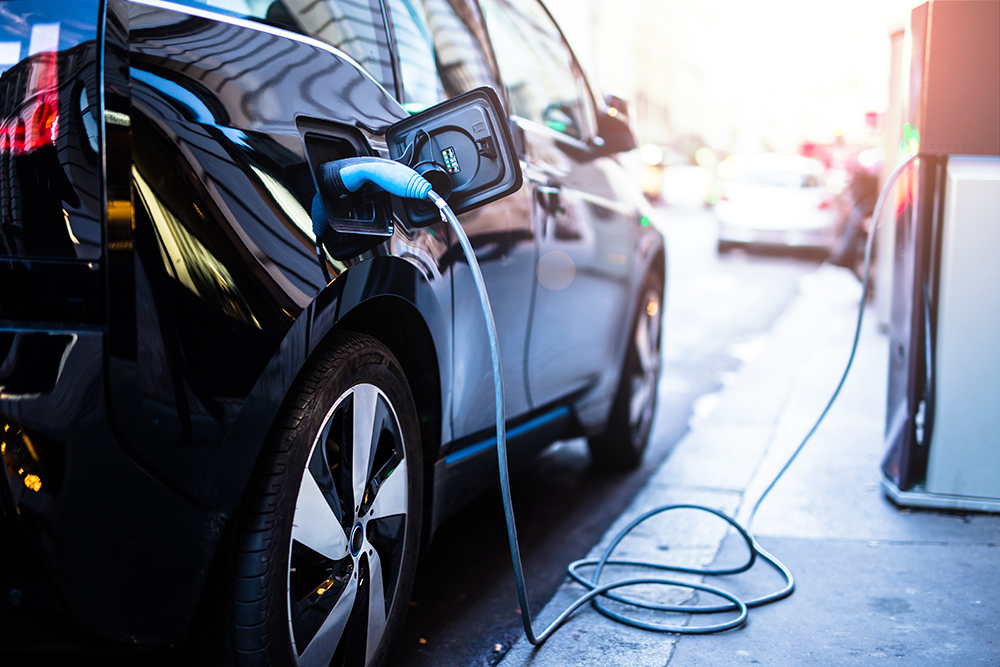
Sponsored by Parker Lord.
Now more than ever, we are seeing a strong trend toward the electrification of vehicles in the transportation industry, including automobiles, buses, trains, off-road vehicles, watercraft and aircraft. In these electric vehicles, long ranges and high horsepower require high power density from their electrical components such as batteries, motors and generators, and the power electronics needed for operation. The trend is focused on smaller, less expensive components that will save space and reduce costs while boosting power efficiency.
A key challenge in developing these components is to manage the heat generated by smaller, high-power devices like on-board battery chargers, power inverters and converters and electric machines. Thermally conductive potting compounds are ideal for rapidly and effectively conducting heat away from power components to the heat sink. The potting compound fills the component enclosure, leaving no air gaps. As a result, heat is dissipated within the enclosure and rapidly conducted to the heat sink, which has enabled substantial size and weight reductions of the finished component.
In Parker Lord’s whitepaper “Thermally Conductive Potting Compounds Enable Higher Power Density Electronics,” they share the results of a study conducted by a team of Parker Lord and Manzanita Micro experts who tested the heat rise of inductors potted in a liquid-cooled aluminum fixture.
Materials used in the study
In this study, they used five silicone potting materials. All the materials are electrically insulative with high dielectric strength and high-temperature stability. These silicone potting materials include:
- Thermoset® SC-400 Silicone Encapsulant: a clear, soft gel with low thermal conductivity (0.1 W/m∙K) used for potting sensitive electronics where high dielectric strength and very low mechanical stress are desired.
- CoolTherm® SC-305, SC-309, SC-320 and SC-324 Thermally Conductive Silicone Encapsulants: Filled silicone potting materials with progressively higher thermal conductivities of 0.7, 1.0, 3.0, and 4.0 W/m∙K, respectively.
These materials are currently being used in numerous applications to protect sensitive electronic components from excess heat, including on-board chargers, inverters and electric motor stators for EVs.
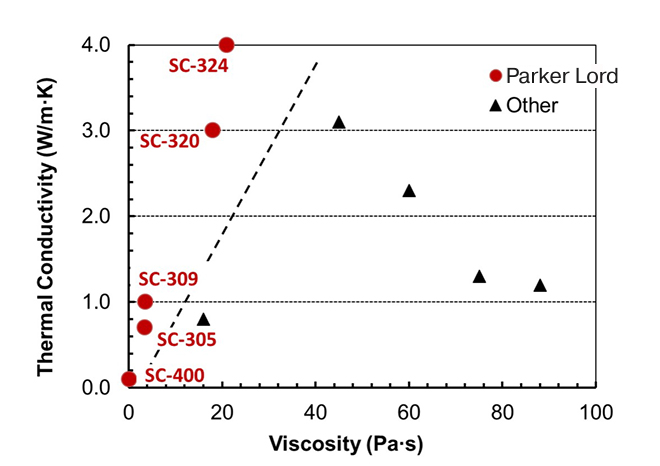
A key differentiating property of their thermally conductive silicone materials is their low viscosity compared to competitive materials with similar thermal conductivity. The lower viscosity allows Parker Lord’s materials to flow and fill voids more readily while providing excellent thermal conductivity. They are also easier to degas, meaning that parts can be potted that are essentially void-free if a vacuum potting process is used.
Inductor potting and testing
The inductors used in this study were made from Micrometals T400-61D high-temperature, magnetic-powder toroid cores wrapped with 62 turns of 10-gauge insulated copper wire, which yield about 500 μH inductance at load. Inductors were potted in custom-made aluminum cooling plates fitted with liquid inlet and outlet ports for connection to an external circulating fluid bath. The five different materials were used to pot three inductors with each material, resulting in a total of 15 potted inductors.
Before potting, each inductor was fitted with a thermocouple to measure its temperature. The location of the thermocouple corresponds to the hottest location in the inductor as judged qualitatively from a thermal camera image of an unpotted inductor under load.
For the thermal tests, each inductor was connected to a Manzanita Micro PFC40X-188 charger passing 9.3 kW and 40 A at 240V input with 0.98 power factor. The power at the inductor was 30W. The aluminum cooling plate was connected to a temperature-controlled liquid bath; each inductor was tested at coolant temperature set points of 25°C, and the typical automotive coolant temperature of 50°C. A second thermocouple was attached to the exterior of the cooling plate to monitor temperature changes during the test; however, the temperature rise of the cooling plate was less than 2°C, even in the most extreme cases.
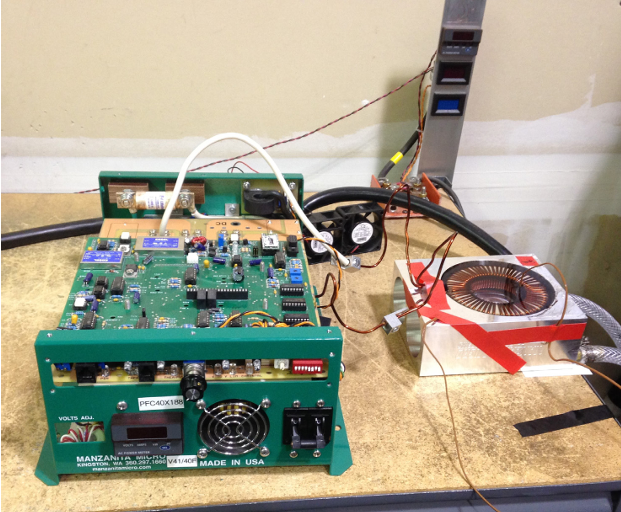
During each thermal test, the temperatures of the inductor and cooling plate were recorded using an Omega Soft data logger. The cooling plate and inductor temperatures were allowed to stabilize with no power. Power was then applied, and the temperature was monitored until the inductor temperature stabilized. The equilibration time was chosen at the point when the temperature reached a steady state (i.e., no further temperature increase took place), and the reported temperature rise was calculated as the final temperature of the inductor minus the initial temperature.
Results
During the study, they used five of their silicone potting materials and tested 15 inductors at least once with several tested multiple times to determine repeatability. Error bars are plus and minus one standard deviation of the data, which includes part-to-part variation and repeatability.
The data show that both the inductor temperature rise, and the equilibration time are independent of the coolant temperature, as the data at 25°C and 50°C are nearly superimposable and within the test variation. It is important to note that the variation becomes much smaller as the thermal conductivity increases due to the more effective thermal connection to the aluminum cooling plate.
Comparing an inductor potted with an insulating material (0.1 W/m∙K) to the most conductive material (4.0 W/m∙K), the heat rise is decreased by about 50°C, and the time required to reach a stable temperature is decreased from nearly two hours to 15 minutes. These significant improvements in heat management enable the development of significantly smaller power electronics.
Dramatic reductions in both temperature rise and equilibration time are observed for inductors potted with thermally conductive materials. The average temperature rise with Parker Lord’s Thermoset SC-400 encapsulant was about 55°C, and the average rise for the company’s most thermally conductive materials, CoolTherm SC-320 and SC-324 encapsulants, was less than 10°C. Even the moderately conductive silicones, CoolTherm SC-305 and SC-309 encapsulants at 0.7 and 1.0 W/m∙K, respectively, provided significant improvements.
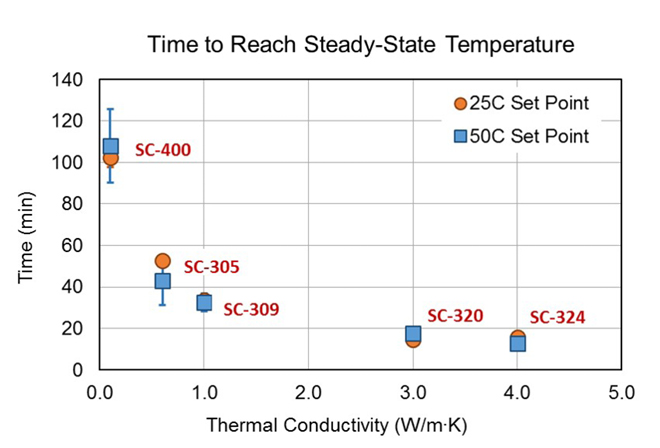
Under different test conditions that would generate a temperature rise much greater than 55°C, the improvement would likely be even more pronounced. Similarly, the equilibration time was also dramatically reduced with the higher thermally conductive materials. With the non-conductive silicone, Thermoset SC-400 encapsulant, nearly two hours was required to reach a steady state, whereas a stable temperature was achieved in less than 20 minutes for CoolTherm SC-320 and SC-324 encapsulants.
This rapid temperature recovery means that heat is dissipated quickly, and components will spend less time at elevated temperatures, thus increasing the lifetime of the components.
Conclusions
Proper thermal management is essential for developing power electronics that are smaller and lighter. And smaller and lighter means higher power density. As the study proves, using thermal management materials provides the unique combination of high thermal conductivity and low viscosity as well as substantial reductions in both maximum temperature rise and the time to reach a stable temperature. Both benefits bring about improvements in efficiency and component lifetime, thereby enabling high-performance power electronics.
Parker Lord’s team, comprised of seasoned technical support and application engineers, is prepared to assist you throughout your power electronic design process. Their vast experience includes working with electric vehicle OEMs and battery companies on cutting-edge technology. However, their scope extends beyond batteries. They are committed to ensuring that power electronics – including inverters, converters, and e-motors – function safely, reliably and efficiently by implementing effective thermal management strategies.
If you’d like to learn more about solutions for power electronics, please reach out to their team.
To read the whitepaper, “Thermally Conductive Potting Compounds Enable Higher Power Density Electronics,” visit their page to download it now.
[ad_2]
Source link